The Relevance of Professional Tank Welding Inspection Providers
The Relevance of Professional Tank Welding Inspection Providers
Blog Article
An In-depth Summary of Tank Welding Examination Specifications and Methodologies for Improved Weld High Quality and Performance
The significance of welding assessment requirements in the manufacturing of tanks can not be overstated, as they serve as the backbone for making certain weld integrity and operational dependability. Various evaluation strategies, consisting of visual assessments and advanced non-destructive screening techniques, are critical in identifying prospective defects that could compromise performance.
Value of Welding Evaluation Criteria
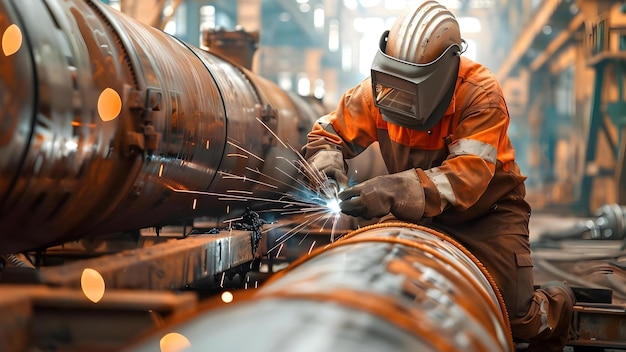
Welding inspection requirements encompass an array of criteria, consisting of material specs, welding treatments, and qualifications of employees included in the welding procedure. By applying these criteria, organizations can systematically determine and rectify possible defects, thereby decreasing the probability of pricey repairs or catastrophic failings. Extensive assessment methods promote a society of accountability and precision, encouraging welders to keep high levels of workmanship.
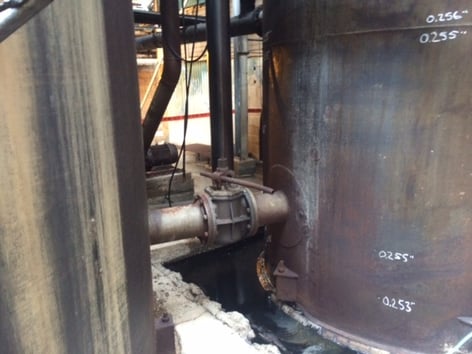
Usual Welding Inspection Methods
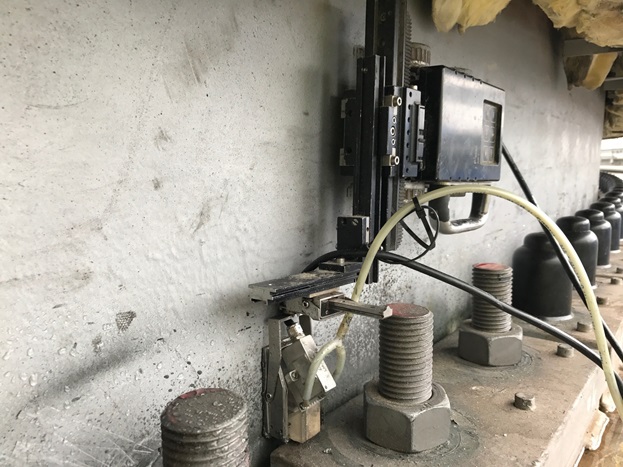

Ultrasonic Checking (UT) is an additional common method, using high-frequency acoustic waves to spot internal imperfections that might not be noticeable externally. This method is specifically efficient for determining voids or incorporations within the weld steel. Magnetic Fragment Checking (MT) is likewise widely made use of, particularly for ferromagnetic products, as it exposes surface and near-surface issues with the application of electromagnetic fields and ferrous bits.
Furthermore, Liquid Penetrant Screening (PT) spots surface-breaking defects by using a penetrant to the weld and afterwards using a developer to draw out the penetrant. Each of these methods contributes to a comprehensive assessment technique, ensuring that welds satisfy the stringent top quality find more requirements called for in storage tank construction.
Governing Specifications and Compliance
Governing criteria and compliance are essential parts in guaranteeing the safety and integrity of welded frameworks in storage tank building and construction - Tank Welding Inspection. These standards offer to establish minimum needs for product residential or commercial properties, welding treatments, and inspection methods, thereby minimizing the threat of structural failures and boosting overall efficiency
Secret companies, such as the American Society of Mechanical Designers (ASME) and the American Welding Culture (AWS), supply guidelines that are widely embraced in the sector. Conformity with these standards not only guarantees adherence to ideal techniques however also meets lawful and contractual commitments, safeguarding the rate of interests of stakeholders.
Governing bodies commonly mandate adherence to specific codes, such as ASME Code Section IX for welding credentials and API 650 for welded storage tanks. These codes detail needs for welding strategies, qualifications of workers, and screening approaches to validate weld stability.
Normal audits and inspections are crucial to preserving conformity, as they assist determine inconsistencies from developed criteria. Non-compliance can result in significant charges, job delays, and security risks. Therefore, a robust understanding of regulative requirements and a commitment to compliance are critical in accomplishing high-quality and resilient welded container frameworks.
Non-Destructive Checking Methods
Just how can the honesty of welded structures be ensured without creating damages? Non-destructive testing (NDT) techniques offer a robust solution, making it possible for assessors to examine weld high quality without jeopardizing the material - Tank Welding Inspection. Among the most common NDT techniques are ultrasonic screening (UT), radiographic screening (RT), magnetic particle screening (MT), and color penetrant testing (PT)
Radiographic testing involves passing X-rays or gamma rays through the weld, producing images that expose structural problems such as cracks or gaps. This method is very useful for evaluating the honesty of complex welds.
Magnetic fragment testing is fit for ferromagnetic products, where magnetic areas reveal surface area and near-surface suspensions. Color penetrant testing uses a fluid dye to his comment is here highlight surface-breaking flaws, making it an efficient method for non-porous products.
Each of these NDT techniques has distinctive advantages, enabling for thorough evaluations customized to specific products and welding procedures. By implementing these methods, sectors can guarantee the integrity and safety of welded frameworks, eventually boosting overall efficiency.
Enhancing Weld High Quality Via Evaluation
Efficient examination plays an important duty in enhancing weld high quality, functioning as an essential checkpoint in the fabrication process. By recognizing possible problems early, assessments minimize the risk of compromised structural stability and make sure conformity with sector requirements. Utilizing a mix of aesthetic examinations, non-destructive testing (NDT) methods, and mechanical evaluations, examiners navigate here can identify concerns such as porosity, cracks, and incomplete fusion.
Executing a durable examination method not just enhances the total top quality of welds yet additionally cultivates a society of liability amongst welders and producers. Normal training and qualification of evaluation workers ensure that they are geared up with the required skills to acknowledge and deal with prospective problems efficiently. This proactive approach minimizes rework and associated expenses, eventually contributing to project effectiveness.
In addition, thorough documents of assessment findings offers valuable understandings right into repeating problems, facilitating continuous enhancement in welding techniques. By leveraging sophisticated innovations, such as automated ultrasonic screening or digital radiography, weld high quality can be enhanced via extra exact assessments. Finally, a strenuous assessment procedure is vital in accomplishing high-quality welds, making sure safety, reliability, and longevity in storage tank construction.
Verdict
To conclude, the application of strenuous storage tank welding inspection criteria and approaches is essential for making sure weld stability and efficiency. By using a mix of visual assessments, non-destructive screening techniques, and adherence to governing requirements, organizations can properly determine and minimize potential issues. Fostering a society of accountability among welders better enhances the high quality of welding processes. Inevitably, these methods contribute to reduced structural failings, reduced fixing costs, and enhanced functional effectiveness within the industry.
Report this page